Lean Six Sigma in a Tight Economy?
By Steven Bonacorsi
We are as uncertain as everybody else is about how bad the economy might get over the next several months. What is certain is that many companies are already taking steps to conserve funds and prepare for a possible recession. We have talked to people whose travel and training budgets have been slashed and others who are doing across the board budget cuts. These are traditional ways companies cut spending as they prepare for tough times. We have also heard of companies reviewing major programs that were scheduled for 2009. Those of us practicing Lean Six Sigma, like those in other disciplines, are forced to consider how bad things could get. At the same time, we should also be thinking about how we can help organizations survive the problems they will face in the months ahead.
One popular Lean Six Sigma argument holds that Lean Six Sigma prospers in both good and bad times. In good times companies want to expand. They expand, acquire other companies, and enter new lines of business. In bad times, companies reexamine their processes and their business models to see how they can save money. In either case, they need Lean Six Sigma practitioners to help them change their processes. It's a comforting thought, and, in many cases, it is actually true.
Consider the financial meltdown that's occurred in the past few weeks. Several financial organizations have merged, willingly or otherwise. Others have changed their status, moving from investment banks to traditional banks, to acquire more government protections. Meantime, governments throughout the world seem focused on introducing new regulations to prevent practices that are presumed to have caused some of the current problems.
Mergers always result in two sets of processes that need to be merged into a common process. Changes in status also require that new processes and business rules be implemented throughout the organization. And, of course, new regulations require new practices and new business rules. All such changes require process analysis and redesign. It may be done by consultants, by process practitioners, or by line managers, but it will need to be done, and it represents a major opportunity for process professionals. Companies other than those in the financial sector probably won't face the major changes that will necessarily take place in that sector, but they will certainly face demands for cost containment and, if the recession deepens, major cost reductions.
On occasions when we have been asked how to sell Lean Six Sigma to management, we have consistently argued that you should not try to sell Lean Six Sigma - as such. In the minds of senior executives, Lean Six Sigma is just another new technology or methodology and is of little or no interest. Instead, we've always urged process professionals to sell productivity and support for whatever changes their organizations need. In the months ahead, those needs are going to be cost containment and then cost reduction. Now is the time for Lean Six Sigma professionals to present management with strategies and plans for containing and reducing costs.
Smart Lean Six Sigma planners are going to want to present a menu of options. An immediate crisis requires actions that can be undertaken quickly and that will yield immediate results. If the crisis lengthens into a long recession, then there will also be a need for changes that require more time to implement but will yield more significant savings. Let's consider these two timeframes independently.
Short Term Cost Containment
Some of the changes companies routinely make are done without much thought, such as cutting travel and training across the board. Smarter companies have a good idea of which processes are yielding the most profit - or are likely to do best in the emerging economy - and cut from those that will be less profitable, while continuing to support the lines of business or the processes that will yield the best results. If your organization has a business process architecture and a good process measurement system, then you can help prioritize intelligent cuts. If you don't, however, it is too late to develop one to help with this crisis on the short term.
Many companies will consider Lean programs to help make quick cuts. Lean vendors and consultants differ on the most effective approach. Some take a broad perspective that captures much of the philosophy contained in the Toyota Production System and they, like other Lean Six Sigma practitioners, will urge enterprise analysis and redesign and cultural change, as well as the elimination of waste in specific processes. Others, however, will focus on the elimination of waste.
The problem with the latter is that it often sub-optimizes overall performance. That is, you may get immediate savings in some areas, but subsequently discover that it is costing you more in other areas. Each company will have to decide the urgency for delivering specific savings immediately versus pursuing a course that will yield a broader and more sustainable savings.
In any case, creating some Lean Six Sigma teams that can move quickly to examine mid-sized processes and suggest quick changes to eliminate waste, is probably an item you should put right at the top of your menu of offerings.
Some companies will find themselves engaged in rapid mergers or in outsourcing. The next three months will be a good time to show that your Lean Six Sigma team can move quickly and get results with a minimum of analysis. This isn't the time for detailed modeling - it's a time for quickly identifying the minimum information required to make smart decisions.
Ironically, it is also a time to think about hiring some consultants. One of the most difficult challenges facing new Lean Six Sigma teams is determining which process problems will yield the greatest ROI. This determination requires considerable experience and you likely don't have time for a lot of on the job experimentation or training. We aren't talking about a lot of long term consulting - we are talking about using consultants to review proposals and provide advice and direction on how best to prioritize activities for implementation of short term gains.
Longer Term Cost Reductions
Broadly speaking, Lean Six Sigma puts an emphasis on broader concerns. It focuses on understanding processes throughout the enterprise and prioritizing and coordinating intervention efforts. The most powerful Lean Six Sigma efforts require trained process managers and monthly measures of process performance. In the best case, Lean Six Sigma leads to more sustainable improvements, but it requires more training and more time to implement.
Similarly Lean Six Sigma products, like most automation efforts, require more time and a larger initial investment to achieve significant ROI. Lean Six Sigma is especially powerful as a way of building agility and the capacity for rapid changes to processes, but a commitment to Lean Six Sigma will require time and experimentation to determine how best to use it.
Most companies, in the next few months, will focus on short term changes to gain immediate savings. Most companies have been running in an expansive mode for the past few years and a good Lean team can almost always identify some quick changes that will save 10-30% of the cost involved in any mid-size process. You probably won't be able to sustain all the savings for more than 6-12 months, but for many that will be an appropriate response to a call for immediate action.
Some companies, however, may not experience the need to simply focus on short term savings. And even those that do will probably not focus exclusively on savings for too long. Smart Lean Six Sigma teams will want to provide an immediate response to executive calls for savings, but will also want to lay the groundwork for more sustained efforts. Thus, even as some specific changes are made, Lean Six Sigma professionals should be pointing out to executives that side-effects and continuing changes will undermine those savings in a relatively short period. Thus, when economic times improve, or when a company is willing to launch a project that aims more at future gains than on immediate savings, the Lean Six Sigma team should refocus on establishing a business process architecture and installing a Lean Six Sigma platform that will lay the groundwork for a more systematic process effort and more reliable long term response capability.
Process professionals are, in essence, support people, and, as such, they must support the immediate concerns of corporate executives. If those executives call for immediate savings, a Lean Six Sigma team should be able to deliver it. By focusing on bloated processes that were created without much thought and/or require lots of overhead, an immediate, significant savings should be easy to provide. At the same time, however, Lean Six Sigma team ought to take advantage of any credibility it develops to push for a more sustainable and comprehensive effort as the economy improves and funds begin to flow more freely, once again. You don't get to be an organization like Toyota by focusing on one-off savings. You get there by creating a culture that focuses on process improvement month-in-and-month-out. Hopefully the current crisis will help Lean Six Sigma organizations to emerge stronger than ever and more focused than ever on installing organization-wide systems for managing continuous improvement.
|
Need a management consultant? Get matched to a local professional near you.
|
Find Management Consultants
|
|
|
|
|
|
|
|
|
|
|
About the Author
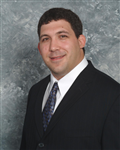 | Steven Bonacorsi, International Standard for Lean Six Sigma 47 Seasons Lane Londonderry, NH 03053 603-401-7047
Contact Author: request info
If you would like to re-print this article, please contact the author.
|
|
|
|
|
|
Editorial Disclaimer: The views expressed in articles published on this website are those of the authors alone. They do not represent the views or opinions of this website or its staff. The articles on this site do not constitute a recommendation or endorsement with respect to any views, company, or product. Authors affirm that article submissions are their original content or that they have permission to reproduce.
|
|
|